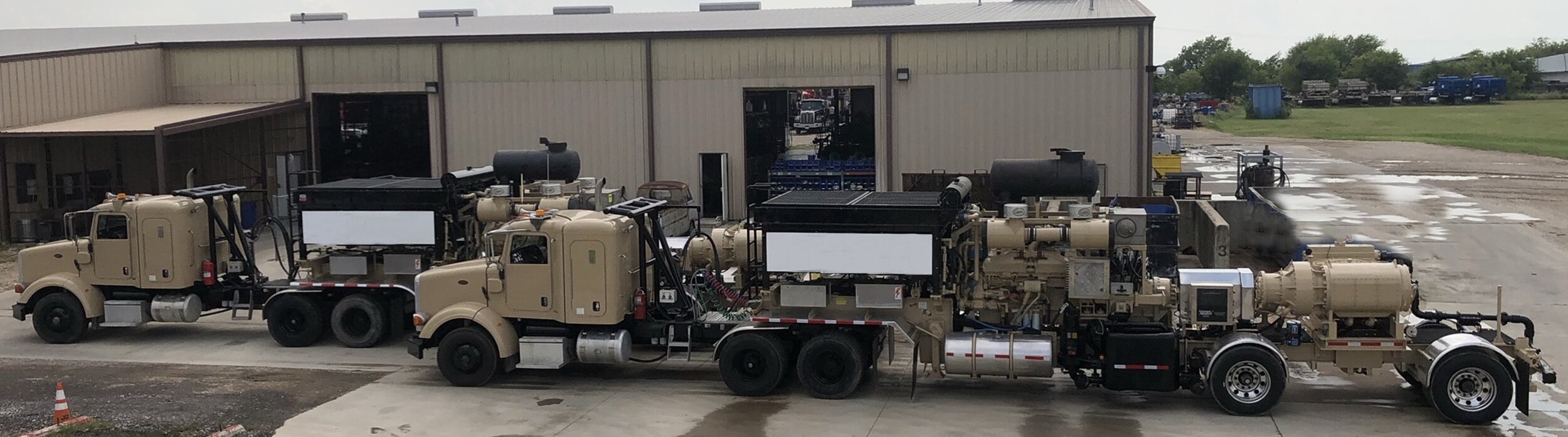
Industry Terminology
GLOSSARY OF INDUSTRY TERMS
HYDRAULIC FRACTURING PROCESS OVERVIEW
The hydraulic fracturing process involves multiple components and stages, including a frac pump, blender, hydration unit, and data van. Here's an overview of the process and the sequence of events:
Site Preparation:
Before the fracturing job begins, the wellsite is prepared to accommodate the equipment and personnel involved.
The frac pump, blender, hydration unit, and data van are positioned strategically near the wellhead.
Fluid Blending at the Blender:
The blender is responsible for mixing the fracturing fluid, which typically consists of water, proppants (sand or ceramic beads), and chemical additives.
The desired concentration of proppants and additives is precisely calculated to meet the specific requirements of the reservoir and enhance fracture propagation.
Fluid Hydration at the Hydration Unit:
The hydration unit is responsible for ensuring the proper hydration of chemical additives in the fracturing fluid.
Various chemicals, such as friction reducers, surfactants, and gelling agents, are added to enhance fluid performance and maintain stability during injection.
Pumping at the Frac Pumps:
The frac pumps pressurizes and pumps the blended and hydrated fracturing fluid down the wellbore.
The high-pressure injection of the fluid creates fractures in the rock formation, allowing hydrocarbons to flow more freely.
Real-time Monitoring at the Data Van:
The data van serves as the control center, equipped with monitoring and frac control systems.
Engineers and technicians in the data van monitor various parameters in real-time, including pump rates, pressure, fluid density, and other critical data points.
Any adjustments to the fracturing process can be made based on the real-time data to optimize the job.
Proppant Placement and Fracture Propagation:
As the fracturing fluid is pumped into the well, proppants carried by the fluid enter the created fractures to keep them open after the pumping stops.
The fractures propagate through the reservoir, creating pathways for oil or gas to flow more freely.
Flowback and Post-Job Analysis:
After the fracturing job is complete, the well undergoes a flowback process where the injected fluids and some naturally occurring fluids are recovered.
Post-job analysis may include well performance evaluations, pressure tests, and any necessary adjustments for future fracturing operations.
This sequence represents a general overview of a hydraulic fracturing job using a frac pump, blender, hydration unit, and data van, demonstrating the coordinated efforts to enhance oil or gas recovery from the reservoir.
ACIDIZING
Enhancing Well productivity and optimizing reservoir performance are achieved through the utilization of acidizing services. This technique involves the introduction of acid solutions into the wellbore, targeting the dissolution of minerals, scale, and other impediments, ultimately improving the flow of hydrocarbons. The applications of acidizing services encompass various aspects:
Well Stimulation:
Acidizing plays a crucial role in stimulating oil and gas production from reservoirs. Over time, factors such as mineral deposits and formation damage can impede hydrocarbon flow. Acidizing effectively mitigates these hindrances, clearing obstacles to enhance reservoir permeability and facilitate increased production rates.
Reservoir Maintenance:
Acidizing services are instrumental in well maintenance, specifically addressing issues like scale and mineral buildup within the wellbore and near perforations. Periodic acid treatments serve to prevent or eliminate these deposits, ensuring sustained and consistent well performance.
Matrix Acidizing:
Matrix acidizing involves injecting acid directly into the formation to create channels or wormholes within the rock. This technique is particularly effective in carbonate reservoirs, where the acid dissolves the matrix, improving reservoir connectivity and leading to a subsequent increase in production.
Fracture Acidizing:
In fracture acidizing, acid is pumped into hydraulic fractures to eliminate debris and enhance fracture conductivity. This process is vital for maintaining or improving the flow of hydrocarbons from the reservoir into the wellbore.
By strategically employing acidizing services in these ways, the oil and gas industry maximizes well performance and ensures the continued efficiency of reservoirs.
CEMENTING
Cementing an oil well is a critical process that involves sealing the wellbore to ensure well integrity and prevent fluid migration. Here are the four major steps in cementing an oil well, formatted for clarity:
1. Wellbore Preparation:
Drilling and Casing: Drill the well to the target depth and insert steel casing to protect the wellbore.
Centralization: Use centralizers to ensure the casing is centralized within the wellbore for uniform cement placement.
Spacer and Flush: Pump spacer fluids and flushing fluids to clean the wellbore and displace any drilling mud.
2. Primary Cementing Slurry Mixing and Injection:
Cement Slurry Design: Design a cement slurry with appropriate density, viscosity, and setting time for the well's specific conditions.
Slurry Mixing: Mix the cement slurry using cement, water, and additives in predetermined ratios.
Slurry Placement: Pump the cement slurry down the casing, and it flows up the annulus, displacing the drilling mud.
3. Cement Setting and Curing:
Waiting on Cement: Allow the cement slurry to reach its initial set before applying pressure.
Pressure Testing: Perform pressure tests to ensure the integrity of the cement job and identify any potential issues.
Curing Time: Allow sufficient time for the cement to cure and achieve its final strength, ensuring a durable seal.
4. Cement Evaluation and Well Completion:
Cement Bond Log (CBL): Conduct a cement bond log to assess the quality of the cement bond between the casing and the formation.
Remedial Cementing: If needed, perform remedial cementing operations to address any shortcomings identified in the CBL.
Well Completion: Proceed with additional well completion activities, such as perforation, if necessary, to initiate production.
These steps collectively represent the cementing process, crucial for securing the wellbore, isolating different formations, and ensuring the safe and efficient production of oil or gas from the well.
COMPLETION SERVICES
Completion services play a crucial role in the final phase of a well's life cycle, commonly referred to as well completion. This pivotal stage, following the drilling process, is essential for preparing the well for production or injection. Completion services are indispensable under various circumstances:
New Well Construction:
Completion services are essential when drilling a new well. Their role involves installing the required equipment and components to enable the safe and efficient production of hydrocarbons or injection of fluids. This encompasses the installation of casing, tubing, packers, and wellhead equipment.
Workover and Well Servicing:
Existing wells may necessitate workovers or servicing to maintain or enhance production levels. Completion services come into play for the replacement or repair of downhole equipment, removal of obstructions, or re-perforation of reservoir zones to optimize production rates.
Well Conversion:
Certain situations may call for the conversion of wells for different purposes, such as transforming an oil well into a gas injection well. Completion services are utilized to modify the well's configuration and equipment to align with its new operational role.
Well Abandonment:
When a well reaches the end of its productive life or becomes economically unviable to operate, completion services are crucial for a proper well abandonment process. This includes sealing off the wellbore to prevent environmental or safety hazards.
Completion services ensure that wells are appropriately equipped, undergo necessary maintenance, and are eventually abandoned when required. Their significance lies in maximizing Well productivity, ensuring safety, and adhering to environmental compliance standards.
PLUG AND ABANDONMENT
The plug and abandonment (P&A) process involves safely and permanently sealing an oil well that is no longer productive or economically viable. Here are the four major steps in plug and abandonment, formatted for clarity:
Wellbore Evaluation and Preparation:
Site Assessment: Evaluate the well site for any environmental or safety concerns.
Wellbore Inspection: Inspect the wellbore for potential issues, including casing integrity and downhole conditions.
Documentation: Gather all necessary well records and regulatory documentation.
P&A Barrier Installation:
Perforation and Cutting: Perforate and cut the casing at specified intervals to allow for the placement of barriers.
Setting Surface Plugs: Install surface plugs to isolate the wellbore from surface fluids.
Cementing Operations: Cement the annular space between the casing and the wellbore to create a secure barrier.
Downhole Plug Installation:
Setting Downhole Plugs: Place downhole plugs at various depths within the well to isolate specific zones.
Cement Squeeze: Perform cement squeeze operations to ensure the integrity of the cement barriers and isolate any potential flow paths.
Verification Logging: Use logging tools to verify the placement and effectiveness of downhole plugs and cement barriers.
Surface Facility Decommissioning:
Equipment Removal: Remove surface facilities, including wellhead equipment, pumps, and other infrastructure.
Site Restoration: Reclaim the well site by restoring the land to its original state or complying with regulatory requirements.
Regulatory Compliance: Ensure compliance with local, state, and federal regulations regarding well abandonment and site restoration.
These steps collectively constitute the plug and abandonment process, ensuring the safe and environmentally responsible closure of oil wells that have reached the end of their productive life.
PRESSURE PUMPING SERVICES
Pressure pumping services are integral to the oil and gas sector, playing a pivotal role across exploration, production, and well optimization. These services entail the high-pressure injection of fluids into oil and gas reservoirs, contributing to production stimulation, well completion, and enhanced recovery rates. Here's a concise overview of their key applications:
Well Stimulation:
Pressure pumping services are commonly utilized for well stimulation, particularly in hydraulic fracturing. This involves injecting a high-pressure mixture of water, sand, and chemicals into the reservoir, fracturing the rock to create pathways for improved hydrocarbon flow. This process significantly enhances production from previously less productive wells.
Well Completion:
During the well completion phase, pressure pumping services are employed to cement casing and tubing in place, ensuring the wellbore's integrity. This sealing action prevents fluid migration between different formations, contributing to environmental protection.
Enhanced Oil Recovery (EOR):
In mature oilfields where primary recovery methods are depleted, pressure pumping services play a vital role in EOR techniques. This includes injecting gases or chemicals to displace and recover additional hydrocarbons trapped in the reservoir, thereby extending the well's life, and maximizing resource extraction.
Reservoir Maintenance:
Pressure pumping services contribute to routine well maintenance, addressing tasks such as wellbore cleanouts and the removal of scale or paraffin. Regular maintenance activities ensure consistent well performance and extend the operational life of the well.
Pressure pumping services are instrumental in extracting hydrocarbons from reservoirs, optimizing production rates, and prolonging well productivity. Their versatile applications make them indispensable tools for oil and gas operators striving to maximize resource recovery and profitability.
WORKOVER SERVICES
Workover services in the context of oil wells involve various interventions to enhance or restore the well's productivity. Here are the four major steps in workover services, formatted for clarity:
Well Evaluation and Planning:
Diagnostic Analysis: Conduct thorough well diagnostics to identify issues affecting production.
Data Collection: Gather data on well history, production logs, and reservoir conditions.
Planning: Develop a comprehensive plan based on the evaluation, outlining the necessary interventions.
Downhole Intervention:
Fishing Operations: Retrieve any stuck tools, equipment, or debris from the wellbore.
Casing Repair: Repair or replace damaged casing to maintain well integrity.
Perforation or Re-Perforation: Create new perforations or re-perforate existing zones to improve fluid flow.
Enhancement and Stimulation:
Matrix Acidizing: Inject acid into the formation to dissolve mineral deposits and improve permeability.
Hydraulic Fracturing: Stimulate the reservoir by creating fractures to increase hydrocarbon flow.
Sand Control: Install screens or gravel packs to prevent sand ingress and maintain well stability.
Well Completion and Testing:
New Completion: Modify or replace existing completion components for optimal performance.
Flow Testing: Conduct tests to evaluate the well's productivity after workover operations.
Artificial Lift: Install or optimize artificial lift systems to enhance fluid production.
These steps collectively represent the workover services process, which aims to maximize the recovery of hydrocarbons from an oil well by addressing various issues that may hinder production.
DRILLOUT
The drillout process is a crucial step in completing a well after hydraulic fracturing. It involves removing plugs or temporary barriers from the wellbore to allow for the free flow of hydrocarbons. Here's an overview of the drillout process and the necessary equipment, formatted for clarity:
Equipment Setup:
Drillout Bit: Choose a specialized drillout bit designed to efficiently remove plugs and debris from the wellbore.
Coiled Tubing or Jointed Pipe: Select the appropriate tubing or pipe to convey the drillout bit downhole.
Surface Equipment: Set up equipment at the wellhead, including a rig or coiled tubing unit, pressure control equipment, and monitoring instruments.
Downhole Plug Removal:
Running the Drillout Tool: Lower the drillout bit into the wellbore, reaching the depth where plugs or barriers need to be removed.
Rotary Drilling or Jetting: Utilize rotary drilling or jetting mechanisms on the drillout bit to disintegrate and remove plugs and debris.
Continuous Circulation: Maintain a continuous circulation of fluid (water or specialized chemicals) to carry away cuttings and prevent debris buildup.
Monitoring and Control:
Surface Monitoring: Employ pressure and flow rate monitoring systems to assess the efficiency of the drillout process.
Real-time Data Analysis: Analyze real-time data to ensure proper removal of plugs and identify any issues that may require adjustments.
Post-Drillout Evaluation:
Wellbore Inspection: Inspect the wellbore using downhole cameras or other diagnostic tools to ensure that all plugs and debris have been successfully removed.
Verification Logging: Perform verification logging, such as through casing inspection tools, to confirm the cleanliness and integrity of the wellbore.
Cleanout and Fluid Recovery:
Flushing and Cleanout: Pump additional fluids to flush out remaining debris and residues from the wellbore.
Flowback and Recovery: Allow the well to flow back, recovering the fluids used during the drillout process, and assessing the initial well production.
Finalizing Completion:
Wellhead Equipment Installation: Install or finalize wellhead equipment for production, such as valves and safety devices.
Flow Testing: Conduct flow tests to evaluate the well's production capacity and overall integrity.
This sequence represents a general overview of the drillout process, and the necessary equipment involved in removing plugs and barriers from the wellbore after hydraulic fracturing, ensuring a clear pathway for hydrocarbons to flow to the surface.